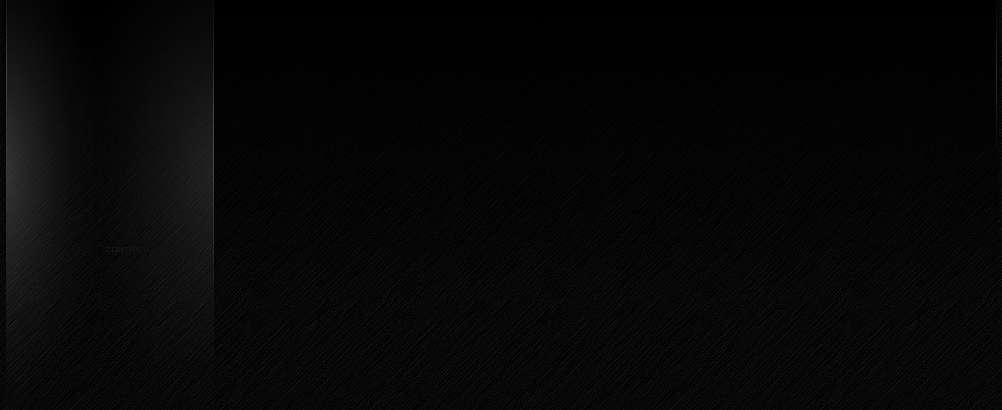
首页〈天火娱乐平台是制约其渗透率快速提升的关键因素。将新能源车系统电压提升至800V后,车身重量、电控损耗均有望降低,整车续航里程呈现提升;此外高压能提高充电功率,加快充电速度并解决补能时间痛点。
因此,高压化趋势是未来新能源车发展的主线之一,有望带来明显的半导体及电子元器件单车增量需求,看好800V产业链上相关国内厂商的投资机会。
全球新能源车渗透率还有较大上升空间。根据IEA数据,2021年全球新能源车(包含插电混动及纯电动)渗透率达到9%,而按地区来看,中国和欧洲渗透率达到15%以上。但纵使在中国本土市场,根据乘联会数据,2022年1-6月中国新能源车渗透率达到24%,其中单月最高渗透率达到28%,我们认为中国及全球的新能源汽车渗透率仍有较大提升空间。
根据Autolist在2021年发布的市场调研显示,消费者购买新能源车最看中的指标由高到底排序为续航里程、价格、充电便捷性及充电时间。总结来看,我们认为续航里程及补能时间成为了新能源车消费者选择产品时的重要考量。
与传统的燃油车相比,新能源汽车的实际续航能力仍是短板,尤其在冬季低温情况下。
用户对新能源车的续航能力关注度较高,但通过简单的增加电芯数量从而提高电动汽车续航里程的方式并不可取。特斯拉创始人马斯克曾在2022年3月于自身社交媒体账号向外界披露,早在2021年年初特斯拉便有能力生产续航里程达900公里的Model S,但这需要通过增加携带电池的重量来实现,带来的负面影响便是让车的加速、操控和效率出现下降,因此该方案没有被采用,最小化每个组件的重量是特斯拉的持续目标。我们看到,如何在不增加电池重量的情况下,增加续航里程是各大新能源车企探索的重要方向。
800V新能源车系统可以通过减重提升续航里程。通过将400V平台提升至800V,由于电流减小发热量降低,线缆变细,电池散热系统及导线V高压平台有利于减轻车身布线重量并增加布线灵活性,从而提升整车的续航里程。
800V新能源车系统可以通过降低电控损耗来增加续航里程。400V的电动机控制器会产生较大的功率损耗,而在相同输入功率条件下,通过提高电动机电压可以减小电流,从而降低热损耗(热损耗= I^2*R)并提升续航里程。我们认为800V高压平台有利于降低电控损耗,增加电池包使用效率,从而提升整车的续航里程。
缩短充电时间是提升客户对新能源汽车满意度亟待解决的问题。如何将充电时间缩短至15min以内从而达到90%以上的客户满意度是提升电动汽车渗透率的重点。
缩短补能时间可以通过提升充电功率(P=UI)实现,而提高电流的方式实现难度较大。提高电流或提高电压两种方式都可以提升充电功率,从而缩减充电时间。目前来看,提高电流的方案复杂性较高,对散热技术要求更高,电线的横截面积越大,布线难度增加、线束重量增加。举例来看,基于400V,600A平台的特斯拉第三代超级充电桩充电功率达到250kW,但其大电流线束的截面积较大,这对一般车企在热管理、BMS相关系统上的相关能力提出了挑战。
我们认为提高电压是缩短补能时长更优的方式,800V平台可以使充电时间降低至20min以内。从技术角度看,我们认为提高电压更容易,可以仅通过改变增加串联电池单元数量的方式来实现(详见电池部分),而且不再面临大电流带来的损耗高、电缆粗、重量高、散热难等问题。如下图所示,800V系统下高功率平台的电动汽车由于充电速度更快,广义的平均行驶速度更快(由于充电间隙的时间缩短)。总结来看,我们认为800V电动汽车平台可以有效提高充电功率,而加快充电速度,有效提高用户的满意度与购买意愿,促进新能源车渗透率的进一步提升。
注:途中所说充电时间均指400km行程的所需用电量 资料来源:E-Technology,中金公司研究部
800V电池电压的提升实现可以通过改变电池组串并联的方式实现。单个锂离子电芯的电压为3-4V,将电池串联可以增大电压,并联可以增大电流。400V汽车电压系统需要约100个电芯串联,比如特斯拉Model 3短续航版的电池包共有4416个电芯,串联数为96;而800V汽车电压系统则需要约200个电芯串联,比如保时捷Taycan的电池包共有396个电芯,串联数为198。
对于纯电整车来说,电压平台的升高并不简单。我们认为,若将新能源车的母线V,则意味着要将高压电器系统的额定电压提升至800V或以上,即核心三电系统(电机、电控、电池)、空调压缩机、PEU(电力电子集成模块)等部件需要在800V甚至1000V的电压下正常工作。
在短期的过渡阶段内,我们认为800V系统可以替代部分400V系统,整车高压系统可选多种实现方案。可量产的、稳定的800V系统不仅仅需要将新能源车的电压从400V提升到800V这么简单,还面临相关高压模块的供应链不配套、充电基建设施不完善等难点。因此,我们认为新能源车厂商在短期的过渡阶段将采用800V与400V系统并存的方式,在获取800V系统部分优势的同时等待相关用电模块的配套升级。
我们认为在电动汽车中800V电机相较400V电机有明显优势,有望优先替进入800V汽车平台。向更高的直流母线电压发展是牵引电机近年来最重要的发展趋势之一,在电动车使用800V电机,虽然会增加一些重新设计的工程量,但是其电磁性能得到改善,利于提高电机功率密度,同时减轻电机重量。我们认为800V电机带来的优势使厂商考虑优先替代400V电机,而400V系统中其他零部件(空调、PTC、车载充电机、DC-DC)可能随着配套供应链成熟以及成本下降后逐渐被替代。我们看到过渡型的800V平台方案主要包括在电机和其他用电器间加入升压器(下图-a),除电机外其余系统均保持400V),将电池和配电盒升压到800V(下图-b),以及将充电枪、电池和配电盒均升压至800V(下图-c)。
注:由上到下分别为图-a/图-b/图-c 资料来源:旺材电机与电控,中金公司研究部
乘用车品牌中,保时捷是第一个量产800V系统新能源车的厂商。保时捷Taycan的量产代表着800V系统时代的开启。
Taycan在设计800V电压平台的时候,受限于各用电模块的开发进度的不同,最初的电压平台不完全由800V用电器组成,整车系统里涵盖了包括800V(动力电池)、400V(空调压缩机)、48V和12V(LFP电池)在内的多个电压系统。由于存在不同电压系统,Taycan采用了800V至400V的DC-DC转换器,并计划在800V的空调压缩机等其他部件面市之时替换掉现有的400V空调压缩机。对于如何兼容现有400V充电桩的问题,Taycan采用额外搭载一台直流车载充电机(BOOST)的方式,先将400V充电桩输出的充电电压升压至800V,再对电池进行充电。
图表:保时捷Taycan 800V充系统架构图及兼容400V充电桩的方案示意
综上所述,由于短期新能源车母线V系统,电动汽车通常会至少引入400V-800升压DC-DC模块(*1)与800V-400V降压DC-DC模块(*1),带来半导体及元器件增量需求。增加的半导体与元器件主要包括功率器件(IGBT/SiC)、电容、电阻、开关、连接器等。
升压模块可安装在400V充电桩上或者汽车内,但考虑目前多数充电桩仍为供400V车型充电,预计升压模块会配备在800V车内。不同的升压方案会带来半导体/元器件的不同需求:1)新增一个升压模块方案(直接采用电荷泵的结构方式实现升压),需要2个电容+1个开关(可能为继电器、熔断器)+连接器。保时捷就采取这种方案,成本较低。一个模块新增电容的价值量约为100-200元,与其它新增成本共计约300元(45美元左右)。2)驱动复用升压充电方案(复用同一个电驱系统,只要改变控制方法,就可以搭出一个Boost升压电路)。现代、比亚迪的汉EV使用了该方案,不会带来明显的半导体/元器件价值量变化。我们认为,远期看,若主流充电桩全部升级成供800V充电的快充桩,则车上的升压模块有望取消。
2)降压模块(车内800V下降至400V、48V、12V供车上不同负载使用)
降压模块一般安装在800V电池与低压电器之间,用以给不同电压的用电模块供电。比如保时捷的降压模块除了将800V降低至12V从而给汽车上的用电器供电外,还需要由800V转400V降压模块,用来给空调压缩机供电。对于一个高压侧为800V的降压模块,需至少使用4个SiC MOS、4个电容(薄膜电容*1,安规电容*2,铝电解电容*1)、2个电感、1个变压器及其他电子元器件,从整体成本来看,我们认为新的降压模块可能会带来150美元左右成本上升。
在上文中我们指出,由于过渡阶段的800V系统需要额外增加升压与降压DC-DC模块,带来成本与车身重量的上升,以及额外的电能损耗,因此我们认为,800V系统的终局是全800V平台。在全800V平台下,新能源车相关半导体、电子元器件单车需求会呈现明显提升,具体来看:
► 功率半导体:SiC器件由于其在高压环境下独特的性能优势,有望随着800V系统渗透率的提升而加速替代硅基功率器件,以当前器件单价来看,主驱SiC功率半导体模块价值量有望达到原Si-IGBT的3倍以上,而OBC、直流充电桩、DC-DC等领域,高压快充平台带来SiC二极管/MOS渗透使功率半导体器件价值量也有望达到Si基的2-3倍不等;
► 模拟芯片:由于电芯串并联方式改变,BMS系统中隔离式CAN收发器及模拟前端芯片有望迎来用量的翻倍,在单价不变情况下,上述芯片单车价值量也有望翻倍;
► 被动元件:800V架构提高了对被动元件耐高压性能的要求,薄膜电容单车价值量有望提升60%以上;而电感侧,800V架构下SiC器件的应用提升了新能源车电力电子系统的工作频率,降低了对电感绕线匝数及整体电感成本,但是高压高频化带来了磁芯材料升级需求;
► 高压继电器及熔断器:高压化趋势有望推动产品性能提升,高压继电器单车价值量有望翻倍,熔断器单车价值量有望提升60%-70%。
功率器件及模块:SiC MOSFET有望代替Si超级结(SJ MOS)及IGBT,市场规模快速增长
与400V电机电控系统方案相比,我们认为全800V动力系统因为更低的功率损耗而更具优势,主逆变器相关开关管耐压等级也需提升至800V。从电机的角度来看,相较400V电动平台,800V电机有更高的功率密度,重量与体积也有所减少,但是由于更高的转速带来的更高的机械应力和防止 PD(Partial Discharge,局部放电)的需要,电机的绝缘性与设计复杂性也会提高。而主逆变器是电机电控系统中最关键的部件,其内部功率半导体器件耐压等级也要随之提升至800V以上。
碳化硅由于其优秀的物理特性,有望随着800V新能源车普及而呈现市场规模的快速增长。碳化硅(SiC)是一种由硅和碳构成的化合物半导体材料,其优点主要是禁带宽度较大,绝缘击穿场强(Breakdown Field)是Si的10倍,带隙(Energy Gap)是Si 的3倍,另外可在250度的高温环境下工作。
在DC-DC领域,在800V电动汽车的DC-DC中,高压侧功率器件的耐压电压水平需达到1200V标准,SiC有望替代传统硅基功率器件,3kW单机功率半导体价值量上升。在1200V电压范围,碳化硅可以在更高的开关频率下工作(DC-DC可以用更小的电感),并且有更低的开关损耗等特点,我们认为SiC MOS的渗透有望对DC-DC带来系统级的尺寸、重量与成本减小。考虑到高压侧四管M1-M4由Si SJ MOS替换为SiC MOSFET,功率半导体价值量由原先15美元左右上升至30美元左右,相比Si SJ MOS方案提升1倍。
资料来源:浙江大学王正仕教授2020年在“第十五届(深圳)新能源汽车核心电源技术研讨会”上的演讲,中金公司研究部
在直流快速充电桩领域,单桩(模块)功率半导体价值量同样呈现上升。配合高压快充的要求,由于充电电流无法持续升高,我们认为未来800V-1000V充电桩有望成为标配,同时,充电功率升高也对充电桩模块的功率密度(单模块输出功率由12-15kW提升至30kW)提出了更高的要求,未来SiC MOS有望对Si SJ MOS实现全面替代。若不考虑双向功能,30kW模块需要30个SiC MOS器件来支撑,以单管8-10美元价格计算,60kW充电桩用功率半导体价值量有望达到3,500元人民币,较现在Si基器件1,500-2000人民币价值量提升1倍左右。
资料来源:浙江大学王正仕教授2020年在“第十五届(深圳)新能源汽车核心电源技术研讨会”上的演讲,中金公司研究部
我们认为,800V电池组串联数量的翻倍带来了BMS(电池管理系统)成本的上升,其中最值得注意的是对电池荷电状态(State of Charge,SOC)进行监控采集的模拟前端(Analog front end,AFE)芯片用量的上升以及隔离芯片的变化。
电池管理系统(Battery Management System,BMS)主要负责对新能源汽车的整个电池组的工作状态进行监测和管理,并均衡控制电池组,对电池组的使用安全、寿命、性能至关重要。车用BMS系统主要为分布式,通过模块化、分级式管理电池单元。新能源汽车的动力电池系统由于充电速度与续航的需求而不断向高容量、高总压、大体积的方面发展,因此在插电式混动、纯电动车型上主要还是采用分布式架构的BMS。
BMS通常包含1个电池监控控制器 (Battery Monitoring Controller,BMC,主控)、1个电池接线盒 (Battery Junction Box, BJB)、多个从控制器(Cell Supervision Circuit, CSC,从控)。在分布式BMS系统中,CSC负责电池组单体的电压检测、温度检测、均衡管理以及相应的诊断,每个CSC模块包含一个模拟前端芯片(Analog Front End,AFE)芯片。而BMC是BMS的大脑,包含一个MCU芯片负责计算电池健康状态(State of Heatd,SOH)与荷电状态(State of Charge,SOC),利用CSC和BJB测量的电池精确数据做出判断与决定,以确保电池的安全性和提高性能,还可以协调BMS的电池均衡功能。传统的BJB主要作为一个机电箱,其中设有分流器、接触器和高温熔断器,是高压电池和动力传动系统之间的链接。
参考Iman Aghabali等人在《800-V EV 动力总成:优势、挑战和未来趋势的回顾和分析》中的研究,我们对BMS主要部件成本做了粗略拆分。从主要部件来看,温度传感器、接触器、主MCU控制器、CAN隔离式网络收发器(或CAN收发器+数字隔离芯片)、电流传感器、AFE模拟前端芯片、接触器/保险丝及其他部件的占比如下图所示。我们测算,假设车型带电量为70kwh,整体BMS成本占电池包整体成本比重为高个位数。
资料来源:Iman Aghabali 等人的论文《800-V EV 动力总成:优势、挑战和未来趋势的回顾和分析》,2021,IEEE,中金公司研究部
资料来源:NXP官网,中金公司研究部,注:MC33771是AFE芯片,MC33664是隔离式网络收发器,MCU是MPC5x MCU系列
4)从芯片角度来看,BMS系统中的芯片种类主要包括AFE(电池采样芯片)、MCU(微控制处理单元)、CAN收发器芯片、数字隔离器等产品。
► AFE(Analog Front End,模拟前端芯片,在BMS中专指电池采样芯片)封装了电压检测、温度检测等模拟电路,被用来采集电芯电压和温度等信息,支持电池的均衡功能。不同厂商生产的不同型号AFE所能采集的电池组数量在3-18组电池组的范围不等。动力电池包是将并联的电芯串联起来形成的。AFE芯片在进行电压采集时,采集的是整个并联的电芯组的电压.以特斯拉的Model S为例,其85kwh的电池包为例,其电池包的额定电压大约为345v,电芯每串3.6v,总串数为345v/3.6v≈96(串),AFE芯片采集这96串电芯的电压。举例来看,NXP的AFE芯片MC33771最多可采集14组电池组的数据,ADI的AFE芯片LTC6813可采集18节电池组的数据。AFE芯片的内部结构区别不大,不同之处在硬件资源(采样通道数量、内部ADC的数量)与针对功能安全要求所设计的架构类型与形式。目前,我们看到AFE芯片领域基本被海外企业垄断。
► MCU:微控制单元(Microcontroller Unit;MCU)芯片又名单片机,把中央处理器、内存、计数器、串口等周边接口都集成在单一芯片上形成芯片级的计算机,为不同的应用场合做不同控制功能。BMS中的MCU芯片可以处理BMS AFE芯片采集的信息并计算荷电状态(SOC)。BMS MCU芯片需要对SOC进行精确计算,需要大量技术与经验积累,我们认为目前掌握BMS MCU成熟方案的仍然是海外厂商,如NXP等;
► CAN收发器芯片:CAN收发器是连接控制器局域网络(Controller Area Network,CAN)控制系统与CAN总线网络的桥梁,是CAN控制器进行总线数据访问的物理接口,负责CAN控制器端数字信号和CAN总线上差分电平信号之间的转换,一般CAN收发器中也集成了数字隔离芯片,来实现高低压电气隔离;
► 数字隔离器:隔离器利用电隔离将低压域系统和高压域系统在物理层隔开,来保证数字和模拟信号间互不干扰以及安全性。在车载BMS系统中,含有低压与高压两种电路,而ADC在高压电路采集的数据传递至低压电路中的MCU的过程中,便需要使用数字隔离器,有时候数字隔离器也会被集成在CAN收发器中。
我们认为,在800V架构趋势下,由于电芯串并联方式改变,隔离式CAN芯片及模拟前端芯片有望迎来用量的明显提升:
► 800V新能源车平台的CAN隔离式收发器芯片价值量有望上升。每个模组(即BMS从控制器)连接一个电池组,在模组之上搭载1个隔离式CAN芯片,经过CAN芯片进行隔离后将数字信号传递到BMS主板,有时CAN收发器也可以部署在图中的编号2位置。我们认为,由于800V电池电压要求下,一般电池厂商通过增加串联电池组数量的方式来达到电压翻倍的效果,BMS从控制器相关的隔离式CAN芯片的数量随之翻倍(有些方案是采用数字隔离+非隔离式CAN芯片的组合来实现,相关芯片用量也呈现翻倍),BMS主板与外部通信的CAN收发器用量及价值量未发发生明显变化。从价格来看,根据TI官网,以ISO1042-Q1隔离式CAN收发器价格为例,其单价在10元人民币(1.6美元)左右,我们认为批量采购价格有望更低。综合来看,我们测算,400V架构下,BMS从控制器相关隔离式CAN芯片单车总价值量约为150元,而800V架构下约成长为300元,提升幅度达100%。
► 800V系统中更多的串联单元需配备更多电压感应通道,AFE的数量有望提升。根据Iman Aghabali等人论文的研究结果,假设一个400V 电池组使用96个串联电池(如Tesla Model S),一个800 V电池组通过提高串联的电池数量来实现升压,使用192个串联电池,每个电池电压感应通道所用AFE芯片价值量为1美元(6.5元人民币)左右,800V电池组的使用的AFE价值量因电池串联数量的提升而提高至192美元(约1250元人民币),提升幅度达100%。
此外,由于电池串联数增加,计算SOH的难度也随之提升,我们认为BMS系统中对主控MCU的要求也呈现提高,但由于用量不存在变化导致单车价值量变化幅度小于CAN收发器及AFE芯片,在此篇报告中我们不对MCU做重点讨论。
整体来看,我们认为800V架构提高了对被动元件耐高压性能的要求,并简化了电感绕线的使用,首先在电容端,800V架构提高了对电容耐高压性能的要求,价值量有望提升。电容主要有两大功能储能和滤波,我们测算传统的400V电动汽车中电容的单车电容价值量约为600元左右。在800V趋势下,随着电压等级提升,母线电容耐压性有望相应提高,带动薄膜电容价值增长。我们对电动汽车中的主逆变器、OBC、DC/DC和外设充电桩4个系统进行了重点分析,通过我们的测算,我们认为800V电动汽车薄膜电容的单车价值量有望增长约67%,有近400元的价值提升空间。
而电感端,800V架构下SiC器件的应用提升了新能源车电力电子系统的工作频率,降低了对电感绕线匝数。电感是滤波电路和功率放大电路中最核心的器件,我们测算其单车电感价值量约为260-670元区间。而在800V升压趋势下,SiC的应用使主逆变器、OBC等设备的开关频率明显提升,因此所需电感的线圈匝数减小,通过我们的测算,我们认为800V单车电感的总体价值量呈现下降,但是高压高频化带来了磁芯材料升级需求。具体来看:
► 主逆变器:逆变器有望动力电池的直流电逆变成三相交流电,电容组成振荡回路,产生一定频率的交流电,电感实现储能、升压、滤波、消除EMI等功能。我们测算,800V平台中,薄膜电容单车使用量不变,电容平均单价有望提升67%左右,即单车总价值量有望提升200元左右,安规电容及铝电解电容价值量变化不大。由于800V新能源车配备了SiC器件,系统开关频率提升,所需电感的体积与价值量变小,但同时对磁芯材料也提出了升级需求;
► OBC:车载充电机(OBC)以交流电源作为输入,输出直流给动力电池,电容的应用场景包括EMI滤波,DC-LINK,输出滤波、谐振腔等,电感主要起到滤波的作用。以主逆变器情况类比,800V平台中,假设薄膜电容的单车使用量不变的情况下,薄膜电容单价提升67%,薄膜电容单车总价值量有望提升近70元,安规电容及铝电解电容价值量变化不大。在高压趋势下,OBC电感使用情况类似主逆变器,假设电感的单车使用量不变的情况下,高压高频系统中电感单价有望随绕线匝数减少而下降,但对磁芯材料也提出了更高的要求;
► DC-DC:通过电容进行滤波,把直流变成电压可变的交流,然后再把交流变换成直流,通过电感进行储能、向负载电容释放能量。800V平台中,假设薄膜电容的单车使用量不变的情况下,电容单价提升67%,单车总价值量有望提升近70元。电感价值量变化情况与主逆变器/OBC所述情况类似;
► 直流充电桩:在直流充电桩应用中,电容保证整流输出电压平稳,吸收来自整流电路的纹波电流;而电感能够有效降低充电桩中电磁干扰和电流带来的噪音,功率电感有望电能转换为磁能进行存储和释放,降低直流电阻、降低交流电阻、改善直流叠加特性。800V平台中,假设电容的单模块使用量不变的情况下,单价随额定电压上升而提高67%,单模块总价值量有望提升50元以上;电感价值量变化情况与上述情况类似。
高压直流继电器是新能源车与充电桩电路开合控制的核心零部件。与传统汽车相比,新能源汽车采用电能作为驱动能源,其电气主回路在通断时产生的高温高压电弧更大,因此对高压直流继电器的灭弧能力提出更高的要求。
新能源汽车800V高压化发展会带来高压直流继电器的价值量提升。800V高压架构下电压和电流更大,电弧更严重,要求高压直流继电器具有更强的耐高压、耐负载、抗冲击、灭弧和分断能力。我们认为这有望带来现有高压直流继电器的触点材料、灭弧技术、腔体设计等方面的升级,带来其价值量的提升。高压直流继电器的使用数量与电动汽车的车型、电路设计有关。从高压直流继电器的配备数量上看,充电桩通常配2只,而纯电动乘用车通常单车配备4-8只(常规主回路/快充回路/普通回路各配2只、预充/高压负载回路各配1只,如下图所示)。
从价格看,高压直流继电器的单价在100-200元区间,由于800V平台的电压更大、电弧更严重,我们预计800V趋势有望使高压继电器的触点材料、灭弧技术、散热技术、腔体布局等方面得到改进,同时单价有望翻倍到200-400元区间。根据贸泽电子数据,泰科电子的900V车用继电器的单价可达875元。综合来看,我们认为高压直流继电器的单车平均价值量有望从1,000元左右提升至2,000元左右。
熔断器起电路保护作用,需要快速有效切断电流。电路发生短路或过载时,通过热效应使熔体熔化或气化,产生断口,断口产生电弧,熔断器通过熄灭电弧来切断故障电路,主要包括熔体、灭弧介质、M效应点、绝缘管壳、接触端子和指示器。
新能源汽车领域主要应用电力熔断器,分为低压保护区和高压保护区。低压保护低于60VDC,用于对车用的低压负载进行保护,如车灯、车窗电机、雨刷器电机、喇叭等。高压保护60VDC-1,000VDC,分主回路和辅助回路,其中主回路包括电池大电流充放电、车辆驱动回路,辅助回路包括空调、PTC、DC/DC、OBC。新能源汽车充电桩是高压保护,应用电压150VDC-1,000VDC,对充电桩直流侧回路进行短路保护。
新能源汽车800V高压化发展会带来激励熔断器、智能熔断器的创新,从而带来高压熔断器的价值量提升。
资料来源:中熔电气招股书,中金公司研究部,注:上表中选取用于主回路保护的EV系列电力熔断器、激励熔断器进行对比
800V电动汽车平台的熔断器单车总价值量有望上升。从数量上看,据中熔电气招股书,充电桩通常配熔断器1只,纯电动乘用车通常单车配备4-8只。电动车单车主回路大部分配备1只,少数2-3只,额定电流300-700A,一般布置在BDU中,部分装在MSD中;辅助回路3-5只,额定电流小于100A,主要应用于空调、PTC、DC/DC、OBC等用电负载的回路保护。从价格看,据中熔电气招股书、中熔电气官网产品和阿里批发网数据,辅助回路熔断器单价在24元左右,400V平台主回路熔断器单价在100-150元左右,800V平台主回路熔断器单价在210-280元左右。
综合来看,我们认为400V平台熔断器单车总价值量约为200-500元,800V平台熔断器单车总价值量约为300-900元,单车总价值量有望提升60%-70%。
新能源车 的续航里程和补能时间问题是制约其渗透率快速提升的关键因素。将新能源车系统电压提升至800V后,车身重量、电控损耗均有望降低,整车续航里程呈现提升;此外高压能提高充电功率,加快充电速度并解决补能时间痛点。因此,高压化趋势是未来 新能源车 发展的主线之一,有望带来明显的半...