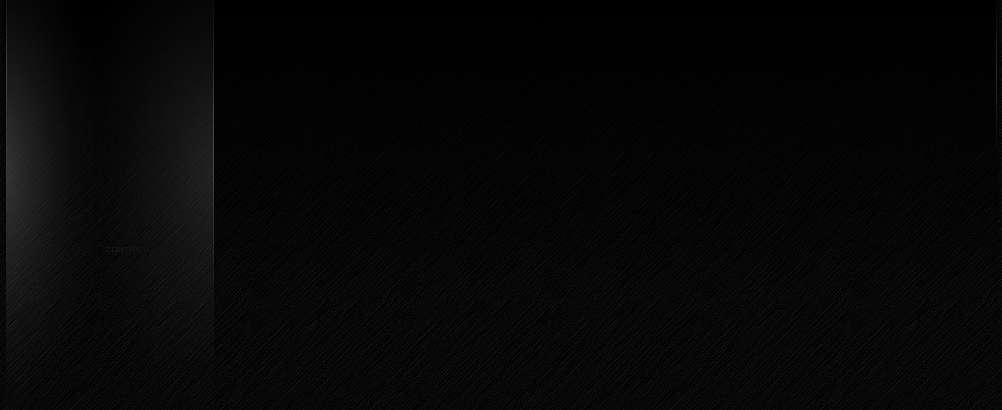
“天健十九载、同心创未来”,3月16日,恰逢“天健龙维成立19周年”暨“江西天健龙维江西生产基地顺利投产”。由汽车评价研究院主办,天健龙维承办的“2024新汽车动力技术趋势论坛”在江西九江举行。
在论坛的圆桌讨论环节中,在中国汽车自动变速器创新联盟秘书长李盛其的主持下,吉利动力研究院院长助理、变速器平台总监谭艳军、上汽集团创新研究开发总院变速箱部总监朱建明、中国一汽新能源开发院传动产品高级主任李卫强、小鹏汽车电驱系统高级总监齐洪刚,天健龙维技术专家谢少宇等5位嘉宾围绕着在新环境下企业如何降本,如何提升新汽车动力技术性能等话题展开了讨论,为参会者带来了一场智慧盛宴。
讨论开始,李盛其秘书长直奔主题,提出第一个讨论主题:“新的一年是以‘电比油低’这样的口号拉开序幕,作为企业该如何应对?”对围绕这个问题,5位嘉宾们阐述了自己对如何控制成本的理解与认识。
首先发言的吉利动力研究院院长助理、变速器平台总监谭艳军把自己的感悟总结为2个关键词——“自制”与“规模”。“控制成本要从两个方面入手——一是要实现核心零部件的自制,因为电机和控制器这样的核心零部件占总成本的比重超65%。”谭艳军告诉大家,“二是要通过平台化、通用化等工作把量做上去,没有规模的支撑,成本是降不下来的。”
上汽集团创新研究开发总院变速箱部总监朱建明对这个问题也认同谭艳军观点,他认为通过设计源头降本是有效、可行的,核心零部件的自主开发、少规模化、平台化能控制成本,并结合上汽集团的产业实践进行了举例说明:“成本是设计出来的,比如上汽自主开发的混动系统五合一控制器,之前控制器技术大多被国外供应商垄断,存在一定溢价空间,现在自主开发的控制器,就能让用户享受到更多让利空间了。”
小鹏汽车电驱系统高级总监齐洪刚也从方法论的维度阐释了他的看法,他认为成本控制涉及产品开发与制造的全链条——“降低成本有着明确的方法论,平台化是关键因素之一,此外还应从设计、制造、质量管控、物流和售后的返修各个领域下手。要把整个流程中没有被意识到的部分都省下来。”
天健龙维技术专家谢少宇从企业在经营实践的经验出发,分享了降低成本的两种方式。“我们一直坚持以客户为中心同步开发、联合设计,从设计入手降低成本。在内部,还有非常重要的一点是制造过程的质量控制。”谢少宇补充,“满足质量要求的情况下,成本压力肯定对我们来说是越来越大的,但是我们致力于把压力转化成动力,驱动公司发展。”
中国一汽新能源开发院传动产品高级主任李卫强则从另一个角度提出了他的理解,在他看来,当前市场上只是在部分车型上实现了“电比油低”,工程技术人员还有很多工作要做。“A级车及以下市场上已经做到‘电比油低’,但B级及以上市场还没实现这一点。B级、C级车用户的需求更多,车辆动力系统应该用什么样的技术来满足这些需求?我们还有很多工作要做。” 李卫强表示,要全面做到“电比油低”,产业链的竞争力还需进一步提升。
目前新能源汽车对驱动电机性能的要求越来越高,从技术趋势看,转速20000rpm的驱动电机将是未来的主流产品,但当前还不能大规模量产。针对这个现象,李盛其秘书长提出了他的第二个讨论主题:“影响20000rpm及以上更高转速的电驱动系统产业的难题是什么?”对此,5位嘉宾也给出了自己的回应。
谭艳军坦言,吉利的团队在开发高转速、高电压油冷电机中遭遇了一些技术难题,团队正在逐一解决。“开发过程中发现了一些以前没有遇到过的问题,比如转速增高后,电机的NVH性能变差,成本也增加了。”他表示,“经过努力,我们克服了这些问题,突破了一些瓶颈,现在已经批产了20000rpm转速的驱动电机,正在做更高转速产品的研发。”
朱建明分析:当驱动电机在20000rpm以上的更高转速工况下,由于系统刚度、系统传递误差、系统润滑等挑战,容易产生NVH及轴承电位腐蚀等问题,需要更多的基础性研究做支撑,零部件企业也面临着基础材料突破、加工工艺创新与设备精度等方面的问题。
李卫强表示,一汽集团自主开发并量产了高速电驱动系统,并在根据已交付车辆的实际运行数据进行产品的迭代,力求为用户带来全生命周期的良好体验。他说:“我们已经由了22000rpm转速的驱动电机,功能是没问题的,我们正在根据使用过程中产生的数据改进其性能、可靠性和持久性,以满足客户全生命周期的要求。”
齐洪刚对高转速电驱动系统的开发与应用提出了不同于前3位嘉宾的看法,他认为不宜单纯以转速高低来评价电机的性能。“‘卷’转速指标对行业发展是有利的,技术上没有太大难度。但如果转速提升后没有得到很好的应用,没有降低成本,那就是没有意义的。”他举例说道,“19000rpm和21000rpm的电机,成本可能会差30块钱,速比增大可能会带来声学光的增加,所以从整体看,这个成本不一定划算,还得综合考虑。”
谢少宇从零部件供应商上的角度给出了自己的理解,他表示,天健龙维现有产品可以满足20000rpm转速的驱动电机的需求。他表示:“高转速电机无论是对于冷却还是对于流液的过滤、杂质控制都提出了新的挑战。我们将努力发挥自己的技术优势,从模具、材料等方面入手与客户一起解决技术难题。”
针对当前越来越流行的混合动力系统,在圆桌讨论的最后阶段,李盛其秘书长提出了一个问题:“应该从哪几方面入手来让混合动力系统的性能最优?”对这个问题,谭艳军和朱建明的看法非常接近,都认为要在设计之初就从系统层面整体考虑,才可能实现性能最优。
谭艳军表示:“要实现性能最优要从整个系统层面去做设计,可以不是最好的发动机,也可以不是最好的混动变速箱,通过合理利用每个子系统的效率最高点,让混合动力系统的运营始终在高校区,那么整个系统结合在一起后就可以做得很好。”
朱建明认为:“要把整个混动系统做到更加高效、性能最优,从产品开发理念上,首先,产品设计开发以用户为本;其次,设计开发过程中要有敢为人先的技术创新及突破。再次,混动系统要满足于整车,做到整车的全局最优,最后,研发团队一定是戮力同心,协同开放。”
李卫强则认为,现阶段要各厂商的硬件性能差别不大,“提分”的关键是软件上。他分析道:“考验的是各个主机厂自己的硬件和软件集成的能力。现在各家零部件的单体效率差不太多,竞争的核心就是软件。”
李盛其秘书长进行了简要的总结,他表示在短暂的互动中,5位嘉宾贡献了自己的宝贵经验与智慧,分析了产业的技术现状与趋势。他认为,当前中国汽车产业正在由大向强转变,希望参会嘉宾是今后的实际工作中多出成果,助力产业发展。
李盛其最后用一句线日的论坛点了题,他说:“我们中国汽车人要在伟大复兴的进程中要做出我们的贡献,要不负这个伟大的时代。”奇亿用户注册,【2024新汽车动力技术论坛】技术专家纵论新汽车动力系统发展趋势