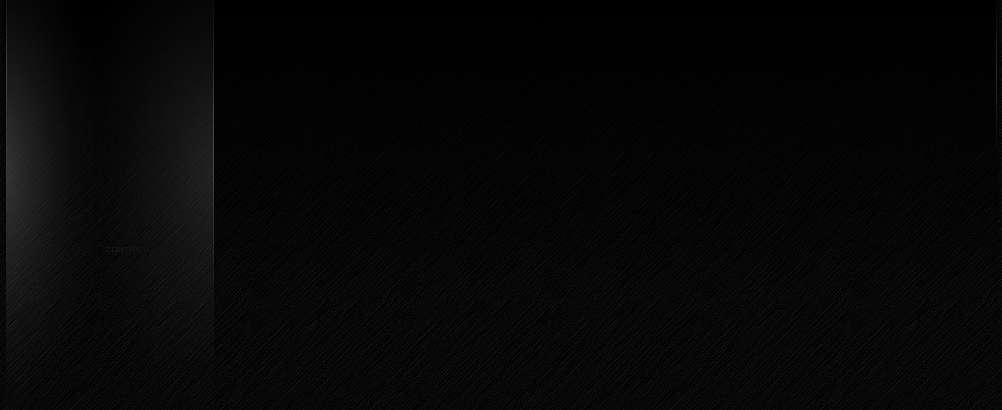
首页;杏福娱乐平台;首页2017年第十七届上海国际汽车工业展览会,几乎每个汽车品牌在新能源汽车领域争奇斗艳,外形炫酷的纯电动超级跑车、纯电动SUV、插电式混合动力汽车或混合动力汽车,事实上,内行看门道、外行看热闹,都称之为新能源,却是大大不同。
俊朗的外形、炫酷的车灯与新能源汽车没有必然关系,更确切地讲,新能源汽车只是在中国的叫法,更确切的称呼是“电气化”,具体分类,文章《被误导多年这才是混合动力的正确分类》已经详述,我们来看看,本次车展琳琅满目的新能源背后,电气化核心有哪些?
专业的电气化是指专门开发的电驱动系统(DHT,Dedicated Hybrid Transmission),着眼于从机电深度融合、控制的深入融合、性能的深度融合来全新开拓设计,典型车企是通用汽车、丰田汽车等。
非专业的电气化,业内被称之为“Add-on(拼凑)”,相对来讲,包括大众、奥迪等相关车型上应用,当然也包括目前上海车展上大部分展出的新能源汽车,我们来看看,他们有哪些区别?
电气化工程是机电深度融合,DHT与Add-on最大区别是整个产品开发思路不同,DHT是从一张白纸出发,全新进行新能源设计,Add-on则是依据现有的的动力总成产品,包括发动机、变速器都不进行大的变更,加一个电机来进行优化,以便于使用高压电池、电机等电气化部件,虽不能最优,也能实现大部分功能。
最早的Add-on概念,是欧洲人针对大众和奥迪提出,因为大众系坚持认为柴油机是未来方向,而放弃了对新能源汽车的深度研发,在经历了柴油发动机排放门事件之后,转型新能源汽车,这个时候来自美国通用、日本丰田的新能源汽车技术已经快速发展,大众采用了P2技术架构,即发动机与变速器之间加了一个电机和离合器,本称之为Add-on。
Add-on最大的缺点是电机及电机控制器集成不彻底,很多优化只能退而求其次。
本次上海车展上,有兴趣的读者朋友可以去看一下对比,比如奥迪展台、大众展台,特征比较明显的Add-on新能源总成技术,我们可以明显地看到高耸的电机控制器、以及交织在一起的橙色的高压线束。
DHT则正好相反,有兴趣的读者朋友,也可以前往通用汽车展台观看,像君越30H、Velite5等车型,均采用的是DHT。驱动电机与整个变速器深度机电集成,电机与齿轮集成在一起,共用油冷系统,电机控制器与电机之间没有三项线束,因为采用了几个短短的接插件就连接在一起,实现了电机与齿轮共舞,这是真正意义的电气化,也是真正意义的新能源汽车核心技术。
事实上,电机与齿轮共舞,这个概念既不是一台电机,也不是一台变速器,而是双方融为一体,成了一个系统,离开电机的变速器无法工作,离开变速器的电机也无法工作,而电机与齿轮的共舞让效率最大化,系统模式最优化,整车集成与布置更优化。
当然,深度融合只是我们看到的内容,DHT相对应Add-on来讲,还有三大利器:
性能更优,对于新能源汽车来讲,性能一般指效率更高、系统更为稳定,通俗地来讲,高耸的线束自身能耗能够消耗电能、Add-on优化模式的短板致使整体效率受损,DHT不仅优化模式更全面,系统部件,例如取消高压线束,利用控制器与电机深度集成,用非常短铜排代替了高压线束,能耗更低,系统更稳定,DHT性能方面有着无可比拟的优势。
成本更低,当然,这些橙色的线束,作为汽车级零件,并不便宜,动辄几百块的价格,对于汽车来讲也是不菲的成本。
DHT电气系统更安全,有两个安全的概念,其一是系统更为稳定,一体化的集成系统连接更为稳固,其二是电气化安全,取消了高压线束,整车震动对于线束没有了影响,系统的功能安全级别更高。
很多人自然而然想到一个问题,为什么有人会采用Add-on概念,而不是君越30H这样的DHT概念。
另一方面,DHT需要足够核心技术,这里面有两个概念,首先要又能力研制AT,因为本质上DHT是电机与齿轮共舞的AT,这项技术貌似没有几家企业掌握,其次是掌握驱动电机的核心技术。
新能源汽车核心技术被称之为三电:电机、电控和电池。电机作为电气化的核心技术,一方面要拥有极高的效率,以通用30H搭载电机为例,最高效率能够达到97%左右,相较于发动机的30%,这个不仅峰值效率高,全工况效率更高,有着比较著名的“双80”,即80%以上的工况效率高于80%,这个概念传统的汽油、柴油车辆远不可能达到。
另一方面,高功率密度,对于新能源汽车来讲,由于增加了驱动电机、电池,整车布置难上加难,扁导线电机功率密度高,以扁导线为主的高工艺难度的电机既成为必选项,也成了很多企业短期内无法逾越的门槛。
以君越30H为例,采用扁导线hair pin绕组,能够将槽满率达到最大化,最大可能地提升了功率密度和效率。所以,很多时候,我们看到很多企业都在谈电动车或混合动力汽车的概念就谈先进与前瞻,扒开之后,才能真正见分晓,目前,我国市场上所谓主流销量的车型中,还没发现应用hair pin扁导线驱动电机。
电机与齿轮共舞,是新能源电气化工程技术的极致,当然除此之外,控制也是重要一环,下篇我们谈谈控制系统的集成如何相互影响。
汽车新闻是一群技术人、媒体人的自留地,欢迎老朋友分享,新朋友扫描二维码关注!
(汽车行业集大成者,涉猎汽车各大领域,任何汽车行业专业技术问题、就业困惑等各种疑难杂症,直接私信老杨就行)
电池是与化学、机械工业、电子控制等相关的一个行业。电池的关键在电芯,电芯最重要的材料便是正负极、隔膜、电解液。正极材料广为熟知的有磷酸铁锂、钴酸锂、锰酸锂、三元、高镍三元。
动力电池是非常“年轻”的产品, 1996年通用推出EV-1采用的是铅酸电池,它是现代电动汽车架构雏形,从铅酸电池到日系混动的镍氢电池,再到现在流行的锂电池,也才20多年。
从第四批《新能源汽车推广应用推荐车型目录》新能源乘用车配置电池来看,32款车型采用了17家企业的电池,其中16家是电池厂商,另外一家是长安新能源的,这说明其它乘用车的动力电池直接外购,包括电芯、电池组与电池管理系统等。
跨国车企,虽然没有自己的电芯,但是它们却坚持自己设计生产电池组件与管理系统,这是为了加强动力电池的核心竞争力。与大多自主品牌的差别是,即使不采用这家的电芯,它们可以换个电芯品牌照样能够设计电池组,核心技术还是掌握在自己手里。
但是我们更关心的是动力电池,也是就新能源汽车中的能量来源,目前动力电池中,镍氢电池面临淘汰,铅酸电池全凭保有量在支撑,故目前以锂电池最为主要。(如下图)
能量密度方面电池肯定不如汽油,但是究竟差别多大呢?一箱50L的汽油可以大概跑600km,续航同样里程的电动车需要多少电池呢?(如下图)
下表列出了四类锂电池的主要性能指标差别。从表中可以看出,四类电池各有优劣。那各汽车厂商究竟是凭什么选择其中某种电池呢?哪种电池又将是未来的主流呢?
数码电子产品对锂电池安全性要求不高,钴酸锂电池最合适3C领域,特斯拉敢于使用此类电池也是未来得到超强的续航能力,但是同时其安全性能要打些折扣。
锰酸锂电池因其不偏不倚的特征赢得动力电池最大的市场占有率,虽然其能量密度不如钴酸锂和三元锂,但其他综合性能相当出色。
如果不是较低的能量密度限制了磷酸铁锂电池,其真的有可能成为动力电池中的霸主。安全性能和寿命这两个关键指标都是顶尖的。
如果说国内把锂电池的发展重心放在了磷酸铁锂电池上,国际动力锂电池行业的新星非三元锂电池莫属,比钴酸锂电池更高的能量密度,成本低于钴酸锂电池,安全性也相当可靠。不同车企对于动力锂电池的选择都有自己的考虑(如下图)
电驱由三部分构成:传动机构、电机、逆变器。目前国内外电动车的传动机构都是单机减速,即没有离合、没有变速。未来各电动车企业将会在传动机构上增加复杂性,同时降低对电机、电机变阻器的需求,即提高性能,降低成本。
电机由三部分组成:定子、转子、壳体,电机技术的关键点在定子、转子。转子即新能源汽车的主驱动电机,它承担了与新能源汽车运动相关的所有功能。新能源汽车的电机有正转和反转,正转即为向前行驶,反转即为倒车。
新能源汽车在正转加速行驶过程中,电机为负扭矩,扭矩的精确意味着新能源汽车加速速度的快慢。当扭矩产生误差时,需要电机来完成的新能源汽车加速,里程数则转变为需要消耗同等能量的电池来完成,而电池的成本相比电机较大,因此新能源汽车电机的效率和性能至关重要。目前汽车专用点击驱动系主要有三类:直流点击驱动系、永磁同步电机驱动系、交流感应点击驱动系。
逆变器是把直流电转变成交流电的设备,若一台电动汽车的逆变器能支持较高电压,则相应的电压充电流较大,功率较大,这意味着同样电流进行充电,充电功率可以等比例放大,即充电时间会缩短。若提高逆变器的支持电压,则相应的充电时逆变器产生的热量会变多,那么就需要解决逆变器中IGBT模块的散热问题,这是提高充电效率的关键问题,目前日本丰田对此研究较深入,例如其加硅碳技术的应用。
新能源汽车电机、电控系统作为传统发动机(变速箱)功能的替代,其性能直接决定了电动汽车的爬坡、加速、最高速度等主要性能指标。同时,电控系统面临的工况相对复杂:需要能够频繁起停、加减速,低速/爬坡时要求高转矩,高速行驶时要求低转矩,具有大变速范围;混合动力车还需要处理电机启动、电机发电、制动能量回馈等特殊功能。
电控方面,对于一般的主机厂来说,真正掌握的只有整车控制器,新能源汽车整车控制器与传统汽车的整车控制器差别并不是很大,它的成熟度也比较高。
此外,电机的能耗直接决定了固定电池容量情况下的续航里程。因此,电动汽车驱动系统在负载要求、技术性能和工作环境上有特殊要求:
1、驱动电机要有更高的能量密度,实现轻量化、低成本,适应有限的车内空间,同时要具有能量回馈能力,降低整车能耗;
2、驱动电机同时具备高速宽调速和低速大扭矩,以提供高启动速度、爬坡性能和高速加速性能;
3、电控系统要有高控制精度、高动态响应速率,并同时提供高安全性和可靠性。
电机电控系统作为新能源汽车产业链的重要一环,其技术、制造水平直接影响整车的性能和成本。目前,国内在电机、电控领域的自主化程度仍远落后于电池,部分电机电控核心组件如IGBT 芯片等仍不具备完全自主生产能力,具备系统完整知识产权的整车企业和零部件企业仍是少数。
通过上面分析可以看出,绝大部分自主品牌仅掌握了整车控制器与三电集成技术,对三电零部件技术却仍是处于没有进门的阶段,毕竟不是一个领域,技术不是一蹴而就的。
而合资品牌方面,没有电芯是它们唯一的软肋,但是通过自己设计电池组与电池管理系统,进而掌握动力电池技术弥补了这个缺陷。技术这种东西是需要积累的。
在2020年前补贴逐步下降甚至之后退出,对于主机厂来说,最重要的工作是如何降低动力电池的成本,也是技术与市场博弈的关键阶段,如果技术受制于人,降成本将难于上青天。
近几年来,新能源汽车销量迎来了爆发式增长,据中汽协数据,2021年新能源汽车销售352万辆,同比大幅增长157.5%。在刚刚过去的2022年,新能源汽车销量更是突破500万辆大关,市场渗透率超过25%,提前3年实现并且超过了《新能源汽车产业发展规划(2021—2035年)》中所提到的“到2025年,新能源汽车新车销量占比达到20%左右”的目标。但需要看到的是,制约新能源车推广的因素还有很多,“里程焦虑”仍然是影响许多潜在顾客选择电动车的主要顾虑。
为了解决“里程焦虑“,业内有“换电“和”快充“两种技术解决方案。相比于换电站高投入带来的巨大成本压力,800V快充被普遍看好。但是与现有的400V相比,800V不仅对三电系统提出了更高的要求,而且对整车高压系统都带来了挑战。以热管理系统为例,为了满足更高工作电压和更大散热能力的需求,开发出耐高压和大功率的空调压缩机是关键。
传统燃油车上热管理主要关注发动机散热和调控舱内温度,而电动车热管理系统不仅用来调控舱内温度,还要调节电机、电池包温度,保证电机、电池工作在最佳温度区间,其中电池热管理能够在电池温度较高时进行有效散热,防止产生热失控事故,在电池温度较低时进行预热,提升电池温度,确保低温下的充放电性能和安全。对于减小电池组内的温度差异,抑制局部热区形成,防止电池过快衰减,提高电池组整体寿命,增加续航里程具有非常重要的作用。
众所周知,冬季续航里程是电动车的最大痛点之一。为了提高电池活性,需要让电池包升温,以前在电动车上普遍使用的PTC(热敏电阻)制热,但也带来续航里程损失过大的问题,数据显示使用PTC制热的电动车在冬季续航里程会减少一半左右。为了解决这个问题,工程师们开发了汽车热泵空调,事实证明热泵空调是解决电动车冬季续航里程的有效方案!试验表明冬季使用热泵空调制热与使用PTC制热相比最大可降低60%能耗,最大带来25%左右的冬季续航里程增加!所以当前新能源热管理系统基本上都是用了热泵技术,热泵系统核心零部件包括电子膨胀阀、油冷器、水冷板、电子水泵、电池冷却器、电磁阀、加热器、热泵压缩机等。其中压缩机是热管理系统的“心脏“,其性能优劣直接决定整个系统的好坏。
为了获得极致的快速储能体验,汽车厂商纷纷将目光投向800V技术,2019年保时捷推出了全球首款量产800V车型Tycan,2021年广汽埃安推出了超充技术的AION V Plus,在2022年小鹏推出了搭载800V技术的旗舰G9,除此之外,几乎所有你能想到的国内外大型车企都已宣布了自己的800V高压架构布局。如大众集团终极纯电平台SSP、奥迪和保时捷高端纯电平台PPE、奔驰MMA平台、宝马NK1平台、通用UItium奥特能平台、现代纯电专属平台E-GMP、吉利SEA浩瀚架构、比亚迪e3.0平台、理想的Shark和Whale平台都会支持800V高压架构。
欲戴王冠必承其重,800V看上去很美,但实现起来并不轻松,对包括热管理系统在内的整车电气架构提出了更高的挑战。
首先是发热问题。虽然800V快充已经降低了大功率充电时的大电流发热问题,但即使是大电压方案,快充带来的发热问题也依然不可避免,只是相对减轻而已。超高的电压使整车的零部件都要承受更大的发热,尤其是电池。在快充条件下,电池内外部的温度差会超过10摄氏度,不均匀的发热分布以及过高的温度将引发粘结剂解体、电解液分解等问题。这会直接导致电池寿命下降、热失控等。这就要求整车的热管理系统需要有更强的制冷性能,要获得更大的冷量和更强的制冷性能,就必须提高压缩机转速。因为有相关研究表明,当压缩机转速提高时,其在单位时间内对制冷剂的吸入量和排出量都将增大,这就使得热管理系统内的循环周期变短以及换热量增加,从而产生更大的制冷量。但是传统的汽车空调压缩机最大转速也就7500转以内,很难达到更高转速,强行提高转速不仅会缩短零部件寿命,还会有带来严重的振动噪音,这对天生安静的电动车来说简直就是一个灾难。
其次是功耗问题,为了迁就高压元器件400V的工作电压,保时捷Taycan通过DCDC转换器将800V降低到400V给整车相关电气系统供电,带来了较大能耗损失,如果这些零部件能够在800V下直接工作,则会带来更多的能耗收益,但这就要求在零部件使用更耐高压的碳化硅材料MOSEFT器件。
由此可以看出,高压快充对热管理系统提出的新要求是很高的,既要有更强大的制冷性能,同时还要有更低功耗控制。作为整车热管理系统的心脏,电动压缩机就成了升级的重中之重。那具体应该怎么升级呢?这时,全球首款量产的采用了碳化硅的800V、12000转电动压缩机出现了。
在家用空调市场,美的绝对是王者般的存在。美的在变频技术方面功底深厚,比如矢量控制、多电阻采样,以及首次采用的20K载波算法等,可以根据环境和人的舒适性要求,把能耗与之进行线性匹配,相当于舒适性、时间和变频三个维度进行匹配,可以说美的在家用空调领域拥有着超越对手的实力。
在车用领域,美的基于自身在机电技术上5500多项专利技术的深厚积累,围绕电机技术为核心的汽车零部件作为突破口,用创新的、高效的技术和产品赋能绿色出行。
面对800V的浪潮,美的工业技术旗下Welling威灵汽车部件开发出质量更轻,功率更高,NVH更平顺的800V 碳化硅 12000rpm电动压缩机,为电动车带来节能,静音的优异体验,为新能源汽车迈入800V时代保驾护航。
首先,在功率方面,800V快充需要更高的转速来满足更强的制冷性能,威灵800V 碳化硅压缩机转速能够达到420-12000rpm范围,在12000rpm下,40cc功率可达14KW的强劲制冷量,超过业内45cc的10KW冷量,达到50cc的产品性能。从而能替代更大排量压缩机,缩小了压缩机体积和重量,实现了小型化以及轻量化,节省整车布置空间,省电节能。此外,通过运用三角循环制热技术,满足压缩机在零下30度超低温环境下,需要同时对电池、驱动系统和驾驶舱等供热的需求。
其次,在材料方面,威灵800V 碳化硅 12000rpm电动压缩机采用了物理特性更优异的碳化硅(SiC)。它具有更强的耐压性和稳定性,加以威灵的超高绝缘耐压技术,将耐压提升到了4000V以上,是800V快充的5倍,保证了绝对的安全性。除此之外,碳化硅三倍于硅的导热性能,让散热效果也更进一步提升。试验对比下来,威灵这套高频率、高效率、耐高温、高导热的碳化硅-IGBT电控方案相较于Si-IGBT在25%负载情况下可以减少80%的损耗。
第三,在能耗方面,威灵采用涡旋压缩结构,高精度装配以及高密度电机,独创了交叠分块电机专利技术,高速轴承技术,高强度铝合金涡盘技术,使功率密度提升了1.1倍,重量减少了1kg,比行业平均水平减轻10%~15%。能效比COP值达2.45,比行业平均水平高5%。
第四,在NVH方面,威灵通过升级双转子结构,解决了转子之心与运动轴心不重合导致的动平衡、噪音等问题。测试数据显示威灵800V 碳化硅电动压缩机在12000 rpm的噪音水平和对手8000 rpm的噪音水平接近,在同样8000 rpm的工况下噪音水平比竞争对手降低3-5dB, 振动下降50%。从而带来低噪安静的驾乘体验。
正是这些卓越的技术性能指标,让小鹏汽车选择将这款威灵800V 碳化硅电动压缩机产品搭载在自己的旗舰小鹏G9上,事实证明小鹏G9的4C车型峰值功率430kW,配合小鹏S4超快充桩可充电5分钟续航200km,从10%到80%仅需15分钟;3C车型从10%充到80%仅需要20分钟,这种极致的体验背后都离不开“超快充、超静音、超经济、超可靠、超转速”的热管理“心脏”!
在汽车电动化浪潮下,快充技术是让电动车补能效率近乎接近于燃油车的重要解决方案。然而,在实现800V快充的路上并不是一帆风顺,对包括空调压缩机在内的整车架构都带来了技术挑战。相信在像威灵汽车部件等一众专注技术研发的高科技零部件企业加持下,未来出行的新时代将很快来临!
欢迎关注@cao sir,一个专注于汽车控制器车载芯片,先进电子架构的攻城狮!
关于新能源汽车核心技术,凌博士想谈谈我们擅长的,也是我们的核心业务之一,那就我们应用于电动汽车里的半导体技术,这里我们重点聊聊主要应用于新能源汽车里的半导体产品碳化硅,它能有效提高电动汽车 充电效率,从而增加续航里程。
关于碳化硅的具体介绍,我们想用一个英飞凌新推出的系列视频“口袋大师”进行讲解,视频里有2位英飞凌新能源车的大神介绍电动汽车对碳化硅如何爱不释手。
若您想寻找更多应用、产品信息或想联系我们购买产品,欢迎点击此处填写您的个人信息及需求,我们将安排专人后续跟进。
新能源汽车的核心一定不是体现在自动驾驶、智能座舱、内饰屏幕,真正体验车企造车技术的是三电系统——“三电”(电池、电控、电驱动)。
动力电池在新能源汽车上一般又称为动力蓄电池,是指为电动汽车动力系统提供能量的蓄电池,主要用于接受和存储由外置充电装置和制动能量回收装置提供的电能,并通过高压配电系统为驱动电机、电动空调压缩机、PTC 加热器等高压用电设备提供电能。
关乎到汽车的续航里程及行车安全等等诸多方面。电池的关键在电芯,电芯最重要的材料便是正负极、隔膜、电解液。
正极材料的稳定性:直接影响到电池的安全性能,乃至整车的安全性能,这也就不难解释某某品牌的电池自燃现象了。
能量密度:电池的能量密度分为质量能量密度和体积能量密度。质量能量密度是指电池单位质量所能输出的电能。体积能量密度是指电池单位体积所能输出的电能。很显然能量密度越大,同样体积或质量的电池能够携带的电能就越多,也就是说续航里程就越大。另外还有一个功率密度,衡量的是电池的瞬间放电能力,功率密度越大,放电能力越强,车辆的瞬间加速能力越好。
通过车企对动力蓄电池的选择也可以间接反应出各车企的追求目标和发展思路,有些更加注重续航里程,有更好的续航体验;有些车企更加注重行车安全,更加注重安全第一的理念。
驱动电机是电动汽车驱动装置的核心部件,应用于各种电动汽车上。驱动电机的性能直接影响到整车性能。
电机由三部分组成:定子、转子、壳体,电机技术的关键点在定子、转子。它承担了与新能源汽车行驶相关的所有功能。新能源汽车的电机有正转和反转,正转即为向前行驶,反转即为倒车。并且还要有很广的调速范围,在能量回收工况时可充当发电机来用。
目前常用的驱动电机有三类:直流电机、永磁同步电机、交流感应(异步电机)电机。
缺点在于:效率低、质量大、体积大、可靠性差。新一代电动汽车已经淘汰该电机
感应电机和永磁结构是相似的,本质都是通过电磁感应原理产生电流。它们最主要的差别就在于转子,一个有磁,使用永磁材料,一个没有磁,通常使用铝或铜材料。
感应电机抗高温性能强,环境适应性更加佳,感应电机虽然最高效率小于永磁电机,但是平均效率表现得更好。不过缺点在于感应电机不容易控制,在研发成本上是增加的,不过在原材料成本上要小于永磁电机。
永磁电机转子的磁场是由永磁体产色的,避免了因生磁导致的电能损耗,而且尺寸和质量偏小,布置相对灵活。
不过现在的一些4驱或者双电机性能取向的车型,会采用两者搭配的方式。因为四驱的电动车架构下当不需要那么高的性能时可以仅让一个电机工作但永磁同步电机由于存在永磁体空载时会产生反拖滞阻碍车辆行进异步电机没有永磁体空载时没有反拖滞,所以永磁同步电机空载损耗会高于异步电机。
电动车极限的动力输出日常使用频率较低在日常行驶低负荷工况下以永磁同步电机驱动为主处于随动的状态,实现近两驱的能耗。在加速工况下双电机最大输出实现四驱的动力,可以给整车带来更好性能体验和综合能耗。
机械传动装置是将电机输出机械能传递给车轮的装置。因为电机一般都具有较好的调速性能,现在的机械传动装置一般都是固定速比的减速机构,不再需要变速器,没有什么技术难度,不做太多介绍。(下阶段的2/3挡电动车专用变速箱其实也取决于车企想不想做和划不划算做而已)
目前电机和机械传动装置基本是机电集成一体化的,可以做到传动效率更高,可靠性更好,质量更轻,体积更小。
电控部分基本相当于车辆的神经中枢,相当于人类的大脑,起着控制整车运行的作用。
新能源汽车电机、电控系统作为传统发动机(变速箱)功能的替代,其性能直接决定了电动汽车的爬坡、加速、最高速度等主要性能指标。同时,电控系统面临的工况相对复杂:需要能够频繁起停、加减速,低速/爬坡时要求高转矩,高速行驶时要求低转矩,具有大变速范围;混合动力车还需要处理电机启动、电机发电、制动能量回馈等特殊功能。
电控方面,对于一般的主机厂来说,真正掌握的只有整车控制器,新能源汽车整车控制器与传统汽车的整车控制器差别并不是很大,它的成熟度也比较高。
此外,电机的能耗直接决定了固定电池容量情况下的续航里程。因此,电动汽车驱动系统在负载要求、技术性能和工作环境上有特殊要求:
1、驱动电机要有更高的能量密度,实现轻量化、低成本,适应有限的车内空间,同时要具有能量回馈能力,降低整车能耗;
2、驱动电机同时具备高速宽调速和低速大扭矩,以提供高启动速度、爬坡性能和高速加速性能;
3、电控系统要有高控制精度、高动态响应速率,并同时提供高安全性和可靠性。
电机电控系统作为新能源汽车产业链的重要一环,其技术、制造水平直接影响整车的性能和成本。
目前,国内在电机、电控领域的自主化程度仍远落后于电池,部分电机电控核心组件如IGBT 芯片等仍不具备完全自主生产能力,具备系统完整知识产权的整车企业和零部件企业仍是少数!
最后,国内绝大部分自主品牌仅掌握了整车控制器与三电集成技术,对三电零部件技术却仍是处于落后的阶段,毕竟技术不是一蹴而就的。而合资品牌方面,没有电芯是它们唯一的软肋,他们更多的通过自己设计电池组与电池管理系统,进而掌握动力电池技术弥补了这个缺陷。
未来随着新能源汽车技术的不断进步,技术瓶颈将逐个被突破,那时的新能源汽车的续航问题,安全问题,充电问题,成本问题都不会再成为车主朋友和车企关心的问题,届时的新能源汽车也会变得更加成熟,市场占比更加广泛。