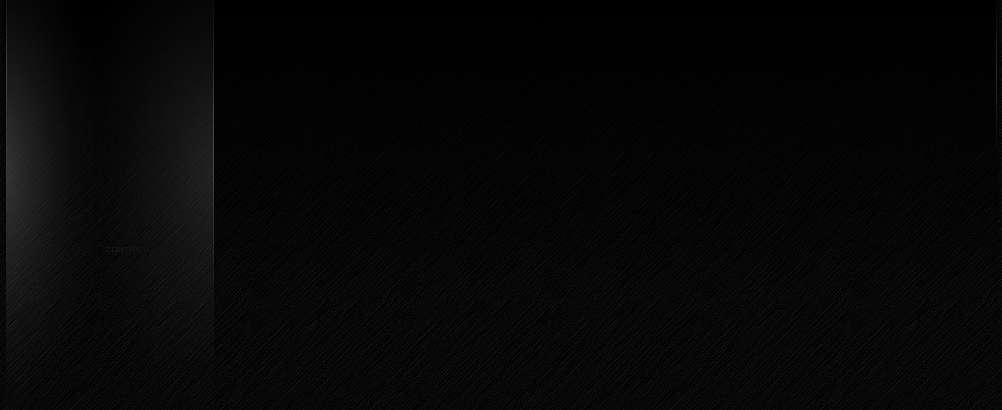
金尚娱乐-注册主页电动汽车驱动电机及其控制系统是电动汽车的心脏,是把电能转化为机械能来驱动车辆的部件。它的任务是在驾驶人的控制下,高效率地将动力电池的能量转化为车轮的动能,或者将车轮上的动能反馈到动力电池中。电能和机械能的相互转化在电机转子和定子间的气隙形成。
电机是一种依据电磁感应原理实现电能与机械能转换的装置。将输入的电能转化为机械能输出的过程叫电动;反之,将输入的机械能转化为电能输出的过程叫发电。
驱动电机分类较多。电动车上目前用到的主要是永磁同步电机,少数用到交流异步电机(特斯拉等)。永磁同步电机需要用稀土永磁材料钕铁硼做永磁体,稀土钕成本较高,造成永磁同步电机成本高,但是永磁同步电机功率密度高。交流异步电机功率密度低,体积大,通过励磁线圈产生磁场,不需要用到稀土永磁材料,成本较低。但是交流异步电机的控制比较复杂。
本文主要介绍永磁同步电机组成的电驱系统的发展趋势。永磁同步电机的结构见下图。
永磁同步电机的功率扭矩特性见下图。可以见到,电机扭矩相应很快,这是电动车起步快的主要原因。
随着对电动车技术的发展,对电驱系统发展提出了更高的要求。电动汽车要求电驱系统具备的特点:高安全、高性能、低电耗、低成本、小尺寸、轻量化。
多合一高度集成、高压化、高功率密度、高安全等级、高性价比、低噪音、高效率、高散热效率
电驱系统集成化有利于减少零部件(高压线、连接螺栓、冷却管路等),降低电驱系统成本,降低装配的复杂度,同时可以降低失效风险,降低故障率。
所以电驱系统从原来的分立式逐步将电机、逆变器、减速器集成设计,有的甚至将DCDC、PDU(高压配电盒)集成在一起。比亚迪海豚更狠,直接集成为八合一:电机、电控、减速器;电源部件三个:OBC、DCDC和高压配电箱;以及电池管理器(BMS)和整车控制器(VCU)。 基于此,不仅给车辆带来了零百加速最快2.9秒,续航里程最大可突破1000公里。
电驱动系统需求:高性能,高安全,高效率,高电磁兼容性。宽禁带功率半导体应用,提升逆变器效率,高功能安全设计,AutoSar安全架构,高电磁兼容性设计与技术手段应用,根据工况分布点进行逆变器硬件与软件的迭代优化设计。
将整车的电压平台从400V提高到800V,从而带来一系列好处。比如可以提高充电功率(速率),降低高压线束的线径,电机体积降低,提高电机功率密度。
高压化的主要挑战是适应高压化的SIC (碳化硅)IGBT设计、高压绝缘设计(耐击穿),车规级的耐高压的功率器件开发,同时高压化也会带来EMC问题。
提高功率密度的途径有很多。上面提到将电机高压化可以提高功率密度。还可以采用扁线绕组,提高槽满率。同时也可以采用多层绕组技术,现在都用到8层导线绕组。
可以采取的措施有:低涡流永磁体技术,超薄硅钢片应用,根据工况分布点的优化设计。
相同功率下,提高电机的最高转速可以降低电机的外径,实现电机降重小型化。一般电机最高转速为12000rpm左右。高速化电机希望将电机最高转速提高到20000rpm。
实现高速化需要攻克的难题:转动系统高刚度设计,轴承旁路导电技术,轴承强制润滑/冷却,转子直接冷却。
还需要开发高速轴承,传统的轴承不能满足高速化电机的寿命要求。车用高速低摩擦力矩轴承的技术目前主要由国外企业垄断。需要研发能够适应承载能力大、转速高而机械损失小的轴承。
基于IGBT的逆变器在高转速大功率电机驱动控制的过程存在开关频率受限、发热量大、效率不高、可靠性有待提升等问题
电动汽车没有发动机那么大的噪音,这时电驱系统的声音就凸显出来,使人听起来很难受。因此应通过各种方法降低电驱系统噪音。例如指定阶次电磁激振力抑制,高频模态识别。
• 冷却效率高,最大程度发挥电机的潜在效能,能够提高电机的功率密度以及转矩密度。
• 绝缘性能好,可以与绕组以及磁性材料接触,直接冷却热源、消除热点,冷却方式直接、干脆,且不导磁、不导电,不影响电机的电磁场特性。
• 相较于水,油的沸点高、凝点低、高温不易沸腾、低温不易凝结,适用范围更广阔,且不易相变。
对于喷油式冷却的电机,外壳不需要设计水道,也不需要风扇及风道,能够减小体积。
• 油品含硫化合物及其他对铜的腐蚀性物质。要确保长期工作不能出现对铜线的腐蚀。
• 应用过程中,防止水分的侵入,,含水量过高会对绝缘材料造成水解,破坏绝缘。
• 粘度过高,低温粘度过大,对油泵压力要求过大,油品在系统中循环较慢,同时对于电机冷却散热效果也差。
• 油冷电机主要散热介质是油,因此油品高温失效要求要高,油品要有良好的高温抗氧化能力,防止高温油泥的生成。
那为何之前电动车都是使用单速变速箱呢?主要一方面还是取决于电动机的本身特点,因为电动机从一开始就能全动力的输出,并且也没有需要怠速什么的,而且电机的转速区间范围要比发动机更高,普遍都能达到7000-10000转以上。而单速变速器就是要将电机的转速降低,并且将动力传递到车轮上,因此电动机在最大输出功率的时候可以保持很宽的转速区间,可以说基本上能满足车辆在面多各种路况下的动力,所以固定齿比的单速变速箱就足够了。而且单档变速器结构简单,成本低廉,在电动车普及的初期,消费者接受程度不高,电池成本高,要尽可能降低其他件的成本。这样才能提高产品的竞争力。
但是对于单速变速箱来说,其也是有缺点的。其在电动车的速度到达极限之后就没有提升空间,在速度上也会受到制约,因此高速经济性下并不会很高。在固定功率相同的状态下,反而采用异步电机的纯电动车在车速方面是更快的,因此装了固定齿比的单速变速箱在速度上达到极限后就不会再提升了。
电机采用变速箱还有一个重要原因,那就是提高电机整体能量效率。电机虽然效率高,但并不是全段效率都高于90%的,低转速大扭矩和高转速中等扭矩这些效率都相对低下,电机会大量发热,续航也会缩短,对汽车的使用寿命是极为不利的,通过合理适配多档变速箱可以使电机更多的处于高效输出区间,延长续航里程,延长电机寿命。
理论上档位越多,越能兼顾动力与高速。但是汽车的设计本身就是一个平衡的过程。档位越多的变速器成本越高。鉴于电机的高效区比发动机高很多,平衡下来一般电机配两档变速器就够了。
电机设计过程中要统筹考虑成本与效率。例如槽满率提高会提高功率密度,但是会带来嵌线工艺困难,制造成本上升。减薄硅钢片可以提高电机效率,但是同时带来成本上升。
诸如这些矛盾都需要在设计过程中平衡。因此,产品设计过程是一个平衡与优化的过程,并不是一定会采用最新最尖端的技术。产品要在大家能买得起的前提下把性能做到最优。